Nuclear gloveboxes
Gloveboxes have been an intrinsic part of nuclear work since the birth of the UK industry. They’ve kept people safe and helped drive nuclear research and development for decades.
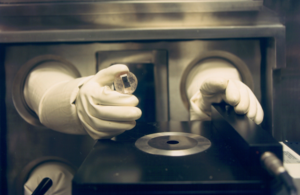
A nuclear glovebox
We have more than 700 gloveboxes at Sellafield, and they help tell the story of the pioneering past, present and future missions on our site.
What is a glovebox?
A nuclear glovebox is essentially a sealed container with built in gloves that allow operators to handle radioactive materials safely.
They vary in size, design and purpose but are commonly made up of a steel frame and panels made of metal or Perspex.
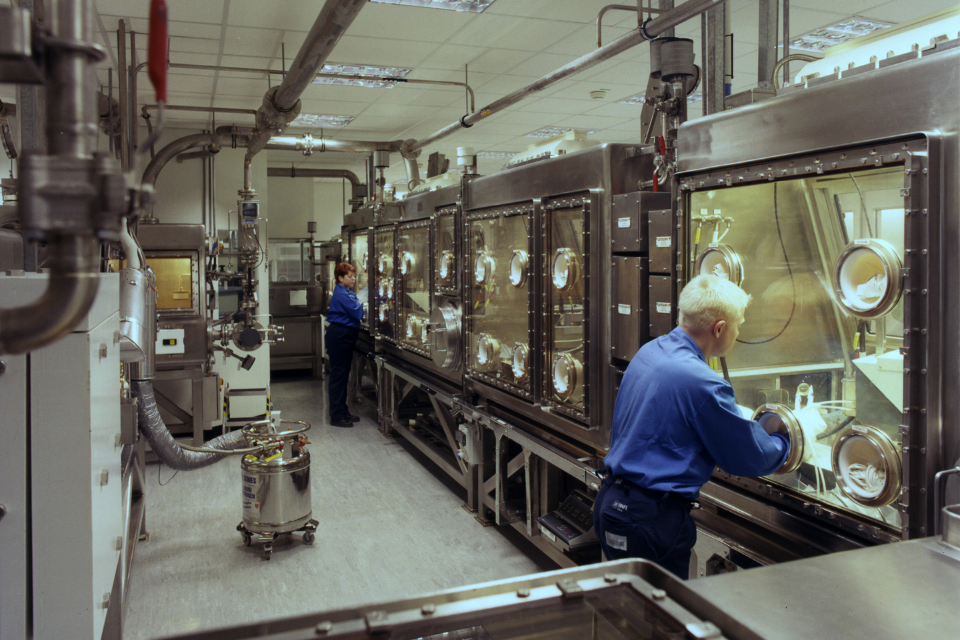
Nuclear gloveboxes on the Sellafield site
Long PVC gloves are built into the box so operators can safely handle nuclear materials without risking contamination. They may also wear additional lead-lined, heat resistant or cut resistant gloves depending on the type of work they are doing.
The atmosphere inside the box is controlled and ventilated, and materials are placed inside via an entry port to maintain containment.
A key part of our clean-up mission at Sellafield is the dismantling and disposal of redundant gloveboxes that were used for historic defence, research, reprocessing, and fuel fabrication operations.
Some are up to 60 years old and in difficult to access places. They can still house contaminated pipework, vessels, cables, valves, or sharp objects that aren’t always visible.
Removing, dismantling and disposing of redundant gloveboxes presents a unique decommissioning challenge but we’re making real progress and learning lessons that can help other nuclear sites.
Analytical Services
Our analytical services laboratories have provided a valuable service to the site for 70 years, with the first built to support defence and reprocessing operations in the 1950s.
Some contain redundant gloveboxes that take up space and pose a potential hazard to workers and the environment.
In September 2024 we successfully removed the first contaminated glovebox from of our oldest and most challenging labs.
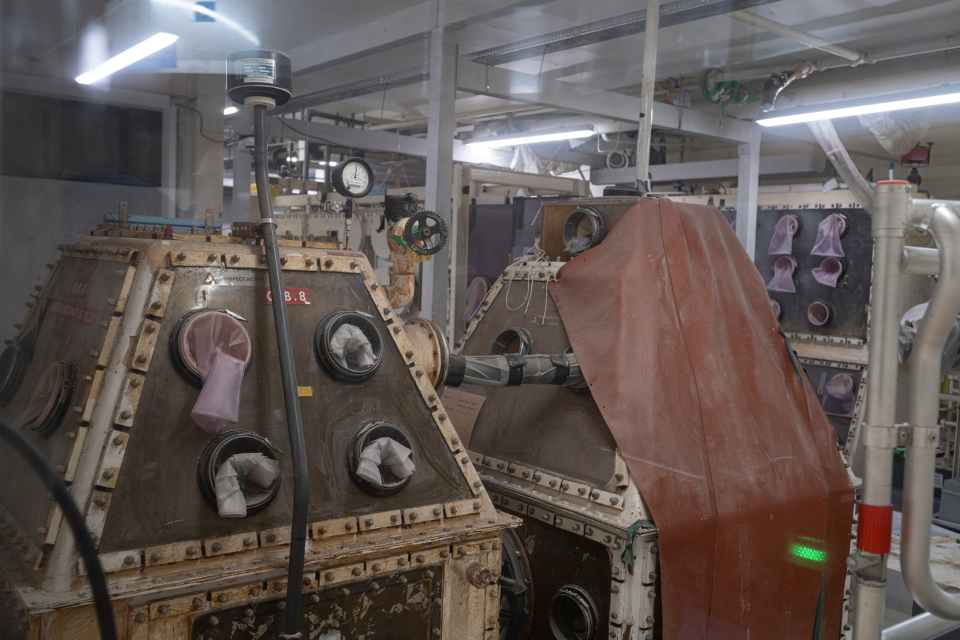
A redundant glovebox in Sellafield's analytical services laboratories
Operators wearing air-fed suits and respirators worked to safely disconnect and cut up the redundant glovebox before sorting it and packaging it for export to a modern waste store.
And in May 2025 we reduced the hazard further by successfully removing a second glovebox, with eleven more to go.
Glovebox work is also at the forefront of the breakthroughs we’re making in applying robotic solutions to nuclear problems.
Sellafield is a test bed for some of the most innovative nuclear technologies in the world and a hub of collaboration with industry, supply chains, and academia.
We’re continually exploring how we can use robots and AI to keep people safe, enhance the work they do, and speed up the delivery of our decommissioning mission.
RrOBO
The Risk-reduction Of glovebox Operations (RrOBO) project is a collaboration between Sellafield and AtkinsRealis with transformational potential for glovebox operations.
In 2023 we demonstrated that a Kinova robotic arm in a containment sleeve could be retrofitted to a glovebox and equipped with a range of tools and sensory equipment to aid operations.
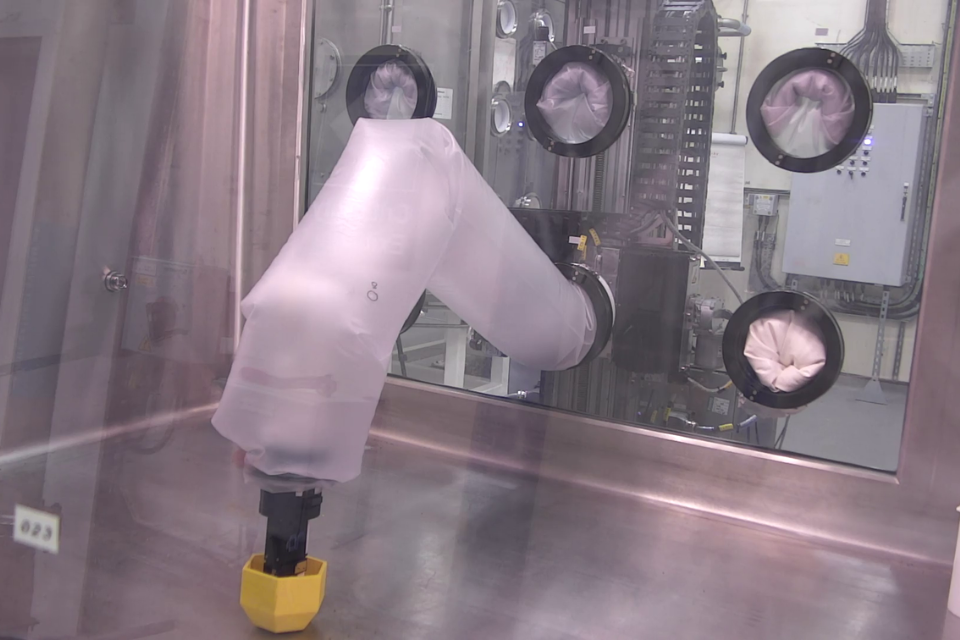
RoOBO deployed in a redundant glovebox
Operators proved they could control the arm remotely to perform a range of tasks including material and equipment moves, swabbing, decontamination, and radiometric scans.
As a result, RrOBO was successfully deployed to decommission a redundant glovebox in Sellafield’s MOX Demonstration Facility in November 2024; the first active deployment of this technology anywhere in the world.
The UK nuclear industry requires thousands of new gloveboxes to support current and future missions in the decommissioning and defence sectors.
We’ll need a pipeline of skilled glovebox operators for many years to come, but it’s difficult work requiring high levels of dexterity and consistent standards.
To help meet this demand, Sellafield is playing a central role in training and equipping the next generation of glovebox operators.
The Glovebox Training Facility
The is a partnership between the UK government and nuclear industry that works to ensure the UK has the skills it needs to manage special nuclear materials now and in the future.
In 2023 it opened the Glovebox Training Facility at Sellafield so learners from around the country can come together to develop their glovebox skills in a safe and controlled environment.
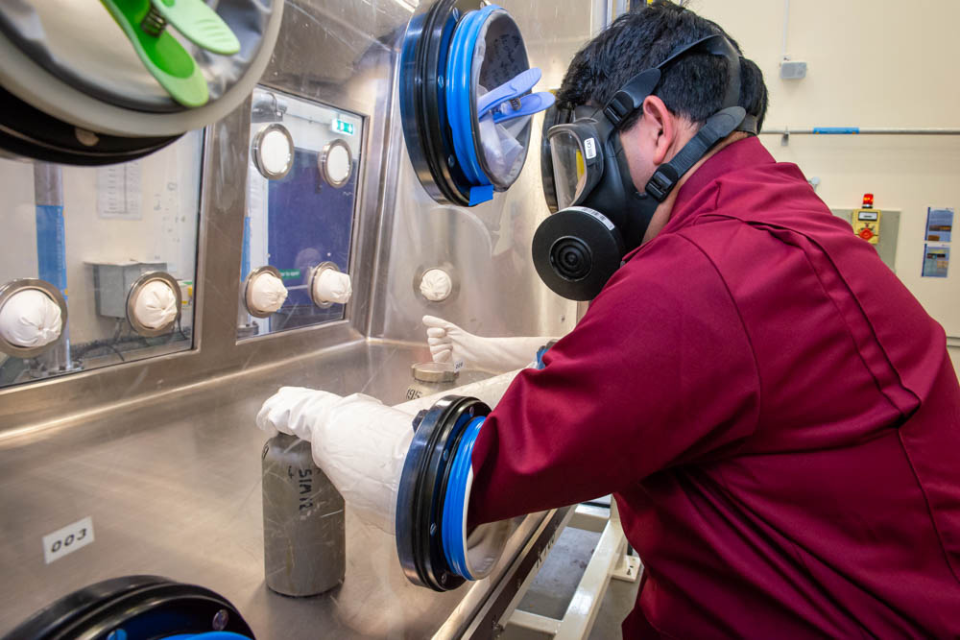
A glovebox operator being trained at The Glovebox Training Facility
This approach has significant benefits in reducing the need for on-plant training and providing a standardised approach across the sector, improving quality and reducing training time by months.
From April 2025, over 170 glovebox operators have been trained there, and in 2025 Sellafield Ltd took over responsibility for the Facility.
Sellafield has an important clean-up mission with a long future. We’re also the custodians of most of the UK’s nuclear waste and over 140 tonnes of civil separated plutonium – the largest stockpile in the world.
It’s a mission of national significance so we’re working with global experts to build the new generation of plants and facilities we’ll need to support the UK nuclear industry and keep the site safe for the next century.
And just as they did for the earliest nuclear pioneers, gloveboxes will continue to play a key role in keeping future nuclear workers safe.
The Sellafield Product and Residue Store Retreatment Plant (SRP)
SRP is one of the largest and most important construction projects on the Sellafield site today.
Once operational in the 2030s, it will receive and repackage plutonium to ensure it can be stored safely and securely for another 100 years.
In May 2025 the project achieved a major milestone when the roof of the main building was finally sealed, making it watertight and ready for internal fit-out.
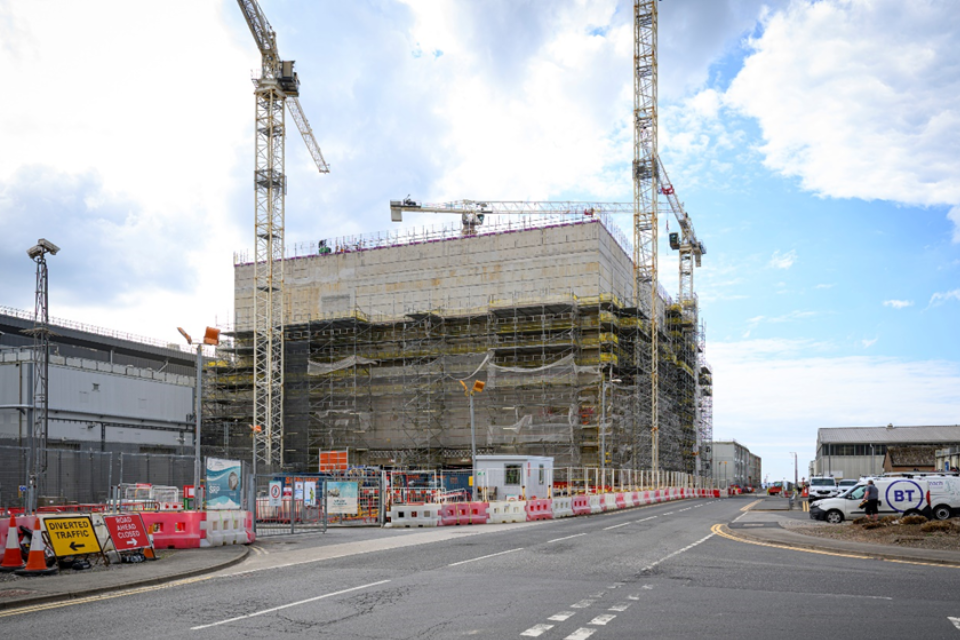
The Sellafield Product and Residue Store Retreatment Plant (SRP) on the Sellafield site
The next phase of the project will include the installation of an array of glovebox systems, most of which will be automated and monitored remotely.
The gloveboxes are currently being manufactured and tested at an off-site facility and the first will be installed in 2026.