UKAEA develops 3D printing for fusion components
UKAEA’s new additive manufacturing – also known as 3D printing – machines offer new opportunities to produce highly specialised components for fusion machines.
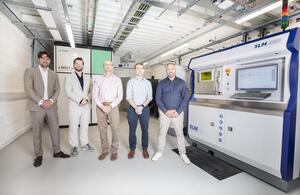
Freemelt (left) and Nikon SLM (right) teams at Central Support Facility launch event with UKAEA's Roy Marshall (centre) - Image Credit: United Kingdom Atomic Energy Authority
The United Kingdom Atomic Energy Authority (UKAEA) has begun using two additive manufacturing – or 3D printing – machines that use complementary methods to manufacture components for future fusion machines.
At its recently opened Central Support Facility (CSF), UKAEA has commissioned an electron beam additive manufacturing machine that will mainly be used to incorporate tungsten into components, alongside a selective laser manufacturing machine.
Fusion can play a key role in a global low carbon energy future. However, the components within future fusion power plants will have to operate under complex and challenging conditions, including extreme temperatures, high neutron loads, and strong magnetic fields. As a result, they require complex combinations of materials and precision engineering.
Additive manufacturing is well suited to producing materials with intricate designs, and in low volumes, making it ideal for a sector such as fusion, where – for the near future – each fusion machine will be highly individual and require bespoke components. As a result, UKAEA believes that 3D printing can play an important role in the future of fusion reducing the costs of this precision manufacturing, and has commissioned the machines to demonstrate two complementary 3D printing methods to produce fusion components.
The eMELT Electron Beam Powder Bed Fusion (E-PBF) additive machine, made by Freemelt, will use electron beam technology to join tungsten in powder-form into solid components with almost 100 percent density. The eMELTmachine will be used to layer tungsten onto other materials such as copper chrome zirconium, stainless steel and Eurofer 97, a special type of steel developed for use in fusion machines.
The SLM280 – Selective Laser Manufacturing – will be used to experiment with how to produce components with the complex geometries and material combinations that will be essential for successful fusion plants. The SLM280 is manufactured by Nikon SLM, provided by Kingsbury Machine Tools, supported by Additure.
Both 3D printing technologies will support the manufacture of plasma-facing components that will be exposed to extreme temperatures during their operational lifecycle. The machines will also reduce the reliance on traditional techniques such as welding, reducing the number of manufacturing operations and joining processes.
Roy Marshall, Head of Operations for Fabrication, Installation and Maintenance, at UKAEA said:
Future fusion power plants will require thousands – or even millions – of components with complex geometries that can withstand the extreme conditions of a fusion environment.
UKAEA believes that additive manufacturing will be essential to developing these components at a scale that makes fusion commercially viable.
We have commissioned two complementary additive manufacturing machines so we can demonstrate that fusion components can be printed at a production scale, enabling the fusion industry to develop components at our facilities that would otherwise be commercially prohibitive.
Using these machines will enable parts and geometries to be produced more efficiently than by using traditional fabrication methods.
Many companies will have either an electron beam machine or selective laser manufacturing technology but having both capabilities under one roof – and able to produce components at scale – is a first for the fusion industry.
Viktor Valk, Regional Manager, EMEA at Freemelt said:
We are honoured to support UKAEA in their important work to advance fusion energy as a commercially viable energy source. The use of Freemelt’s industrial machine eMELT to produce tungsten plasma-facing components exposed to extreme conditions in fusion energy machines, marks an important step in applying our E-PBF technology to fusion energy development.
Christoph Barefoot, Regional Business Director UK & Nordics, Nikon SLM Solutions, said:
Fusion represents the future of energy – but it can only be realized through bold innovation and trusted collaboration. At Nikon SLM Solutions, we are proud to support UKAEA’s mission with our industry-leading Selective Laser Melting technology, helping make complex, high-performance fusion components not just possible, but scalable. With this milestone, we move one step closer to commercial fusion – and a more sustainable tomorrow.
The CSF brings together this technology with purpose-built workshops into one building – alongside UKAEA’s Manufacturing Support Team and Special Techniques Group – to enable collaboration between manufacturing teams and to support fusion research and development. UKAEA is now working to prepare commercial partners for the large scale production that is essential for the fusion energy plants of the future.
Both machines will now start the work of producing challenging geometries and undertake experiments exploring the properties of additive manufactured materials. This work will be followed by initial stages of manufacturing involving tungsten and copper chrome zirconium layering.